References
Molenbergnatie | Innovative transport management
Molenbergnatie commits to innovative transport management with Suivo. Molenbergnatie resolutely chose to modernize its business processes. "Innovative transport management in a digitizing end-to-end supply chain."

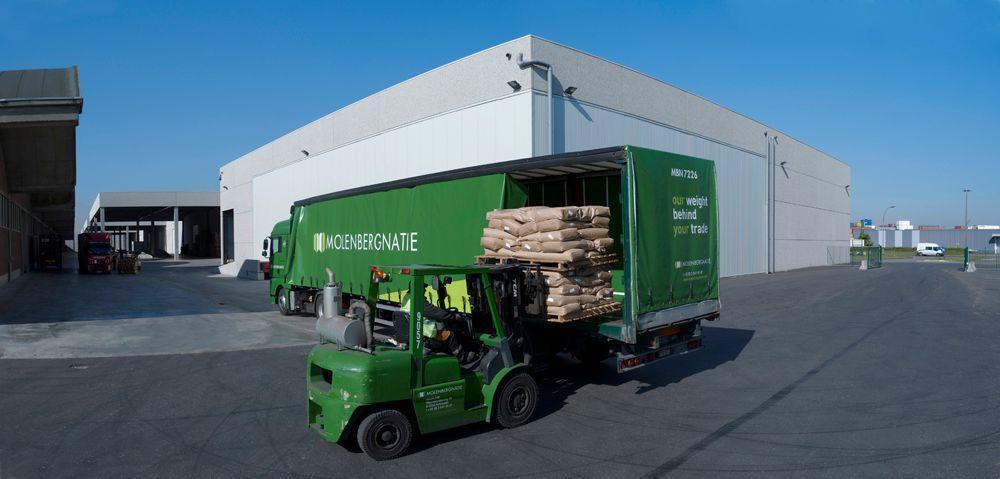
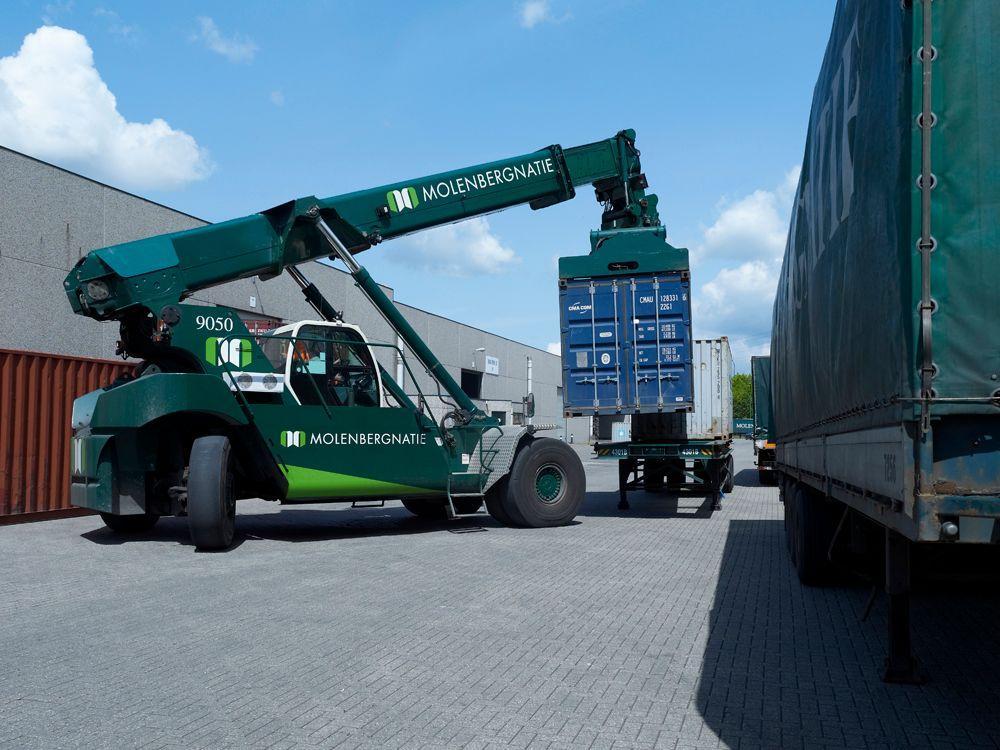